- ULTRA ENERGY – EFFICIENCY COMPARISON - kW energy to HEAT raw material from ambient to required drying temperature is the same for all drying processes. kW energy to DRY raw material is where the difference occurs, comparing ULTRA dryers to all Desiccant dryers.
- ULTRA LOW ENERGY – OPERATING COST SAVINGS - A process running at 220lb/h (100kg/h) can typically see a kW difference of 41 Watts/lb (92 Watts/kg) with ULTRA dryers versus generic desiccant dryer.
- SAVE ANNUALLY – ULTRA saves $6,500 annually at an example rate of 220lb/h (100kg/h) – whilst doing the exact same job. ULTRA delivers savings year on year for its full life cycle.
- ULTRA LOW ENERGY – DYNAMIC SOFTWARE - Temperature Sense Control – temperature is controlled efficiently with energy saver as standard.
- AUTOMATIC REGULATION - Heater and air flow are automatically regulated to ensure only the required amount of heat and air flow are used to bring material up to temperature.
- ULTRA QUICK DRYING- ULTRA dryers place materials under vacuum to dry rapidly, versus long exposure to desiccant hot dry air flow. Normally, ULTRA dries material 6 times faster than conventional desiccant dryers.
- ULTRA FAST DRYING - provides quicker start-ups.
- ULTRA LOW ENERGY COMPONENTS - No regeneration process, no added energy used.
- SMALLER COMPONENTS - ULTRA uses only one smaller blower and heater sized for smaller volumes and faster drying times.
- COMPACT HEATING HOPPER – less material in process, less energy used, easier cleaning.
- MINIMAL MAINTENANCE – no scheduled maintenance requirements and no consumables.
- ULTRA LIVE THROUGHPUT MONITORING - Load cells monitor the vacuum chamber and retention hopper and provide live materials usage data. Data allows the drying rate to efficiently follow and adjust according to the dryer consumption rate.
- EFFICIENT DRYING - ULTRA live data makes for ULTRA efficient drying.
- ULTRA FAST RETURN ON INVESTMENT - ULTRA dryers quickly pay-back in the short term and continue to provide energy reduction cost savings in the long term. Energy usage – one Desiccant day = one ULTRA week.
- INCREASED PRODUCTIVITY – plus, reduced start-up scrap rates and reduced energy usage for the same period.
- AUTO STOP FEATURE – Simple cleaning / Shutdown. Load cell data allows an Auto Stop time to be set. The dryer finishes at the time set with no material left inside – this allows quick cleaning and startup of new materials.
- DYNAMIC DRYING FEATURE – EFFICIENT DRYING - Load cell data automatically adjusts drying rate to process rate – only dries what’s required, minimizing kW per lb / kilo.
- AUTO START FEATURE – SIMPLIFY STARTUP - Another standard feature that allows material to be scheduled and ready without operator intervention.
- ULTRA GREEN – REDUCED ENVIRONMENTAL IMPACT – ULTRA’s low Energy usage significantly improves sustainability by reducing a processors Global Warming Potential (GWP). On a process running 220 lbs/hr (100 kg/hr) an ULTRA dryer provides savings of 54,120 kW a year*. Year on year.
SYNCRO GROUP
Ideal partner for plastics processors who require innovative technology to gain a competitive edge.
ULTRA Dryers
The first ULTRA Low Energy Dryer for all plastic raw materials.
The first ULTRA Low Energy Dryer for all plastic raw materials.
ULTRA dryers are based on unique technology for use in the plastics processing industry. ULTRA dryers quickly pay-back in the short-term and continue to pay dividends through energy reduction in the long term.
Ultra-low kW energy usage – fast ROI and savings for a lifetime.
Category: DRYER
Tags: Dessiccant, Drying, drying resins, Energy saving, Extrusion line, Industry 4.0, Low energy dryier, Maguire, Maguire + Syncro, plastic material, ULED, ULTRA, Vacuum Dryier, VBD
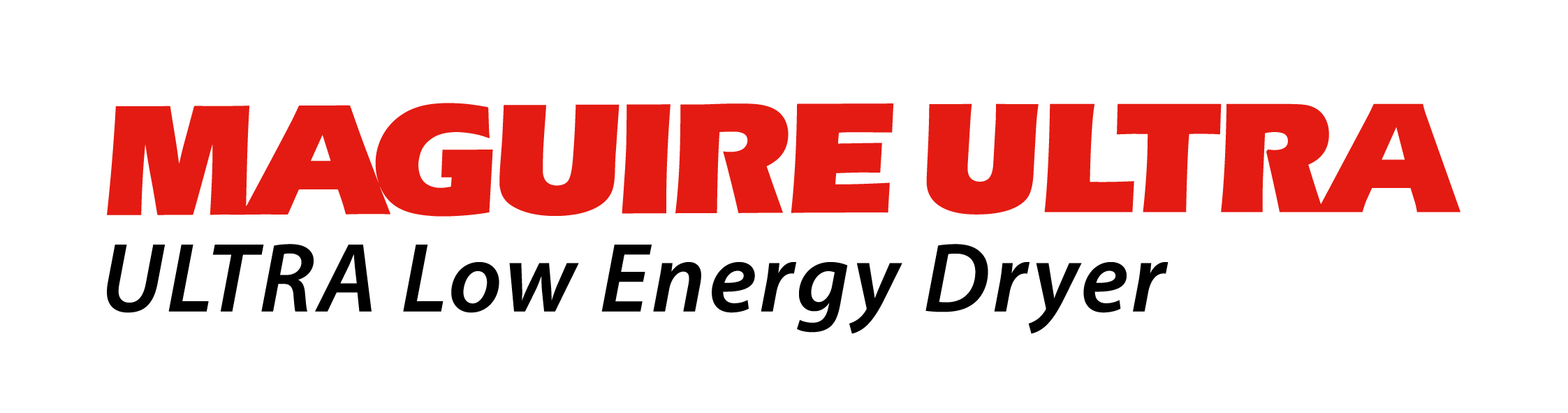