- AUTOMATIC MANIFOLD UNIT - SYNCRO's automatic manifold manages indipenendently material inlet from storage units and outlets to hopper loaders. The operator only simply need to set the material corrispondance from inlet and outlet through a simple graphic display. The positioning system guarantees an accuracy of 1/50 of a degree, the back slash error which a common issue with traditional systems is eliminated thanks to the exclusive drive system, no additional set-ups or adjustments are required after the installation for the rest of the manifold's life.
- High speed positioning.
- No more operator mistakes guarantees the right material with the right user.
- High Speed changes.
- With the RFID option, no more operator’s mistakes are possible and guarantees conveying the right material to the right location.
- Upgradable in the future. High flexibility. High flexibility.
- No vacuum loss due to the unique pipe clamping.
- Less pipe work.
- Less maintenance
SYNCRO GROUP
Ideal partner for plastics processors who require innovative technology to gain a competitive edge.
Synet
Syncro Group stand alone and centralized conveying system
SYNET multiple manifold with quick clamping system for easy pipe matching, along with the option of RFID sensors is providing a “zero error” material identification.
SYNCRO has developped both stand alone and centralised conveying systems which are totally integrated to the SYNCRO dosing units range of products. These conveying systems are equipped with commercial modular PLC electronics to guarantee simple integration to all of SYNCRO’s machines.
SYNET is a standalone centralized vacuum loading system and it is an alternative to SYLINK when SYNCRO
blender are nor supplied or just simply when multiple lines have to be managed.
Different type of pumps are available for SYLINK and SYNET to be configured accordingly to the output, number
of lines, number of components and distances from the silos.
Easy and flexible system suitable for future upgrade in adding pumps and receivers in all sizes.
Dedicated and specific programs for material.
– Easy and economic application/commissioning of the SYNET.
– Easy to program from HMI.
– Prepared for future supervision.
– Possible to up grade with twin piston valve line cleaning.
– Possible to up grade with the digital panel display.
– Possible to up grade with discharge level sensor or continuous level sensor to determinate the material quantity inside the hopper.
– Future developments.
– Blower Speed control according to material types.
– Two vacuum units loading material from the same manifold branch.
– Bar code systems to identify quickly & easily material information.
– Interface with dryer to turn off heating to save energy.
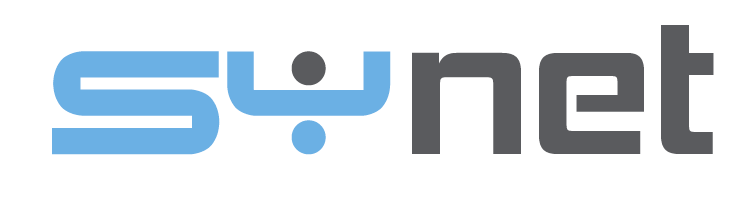