- Minimal power consumption & the highest output / kW of installed power in the market. Giving you lower running cost and therefore the quickest return your on investment with paybacks in as little as six months.
- Low shear, minimum process dwell time and the absolute minimum of material degradation. Means you can recycle all of your scrap material into high quality pellets, reducing your material costs and improving your profitability.
- Slow rotating shredder technology and unique screen design. Requires no cooling water of the rotor or transfer system, reduces maintenance and costs, therefore improving your profitability.
- Smallest footprint recycling machine available on the market. Minimal floor space is required freeing up valuable floor space for other applications.
- ANCILLIARES AIR or WATER COOLED PELLETISER Air or water pelletisers, the material or output being run determine the type of pelletiser needed.
- TRIM BASKET For feeding inline trims into the shredder.
- REELFEED Used to feed off-spec or scrap reels into the shredder.
- ELEVATOR & METAL DETECTOR Used to convey loose, pieces, reels, lumps, in fact any type of scrap into the shredder.
- SCREEN CHANGERS Manual or automatic systems available, used when running offline products i.e. reels, flake etc.
- VACUUM DEGASSING STATION Single or double venting systems available to allow you to run printed or hydroscopic materials.
- DTEC A pellet detection system to advise if there are issues in the pelletiser.
SUITABLE MATERIALS
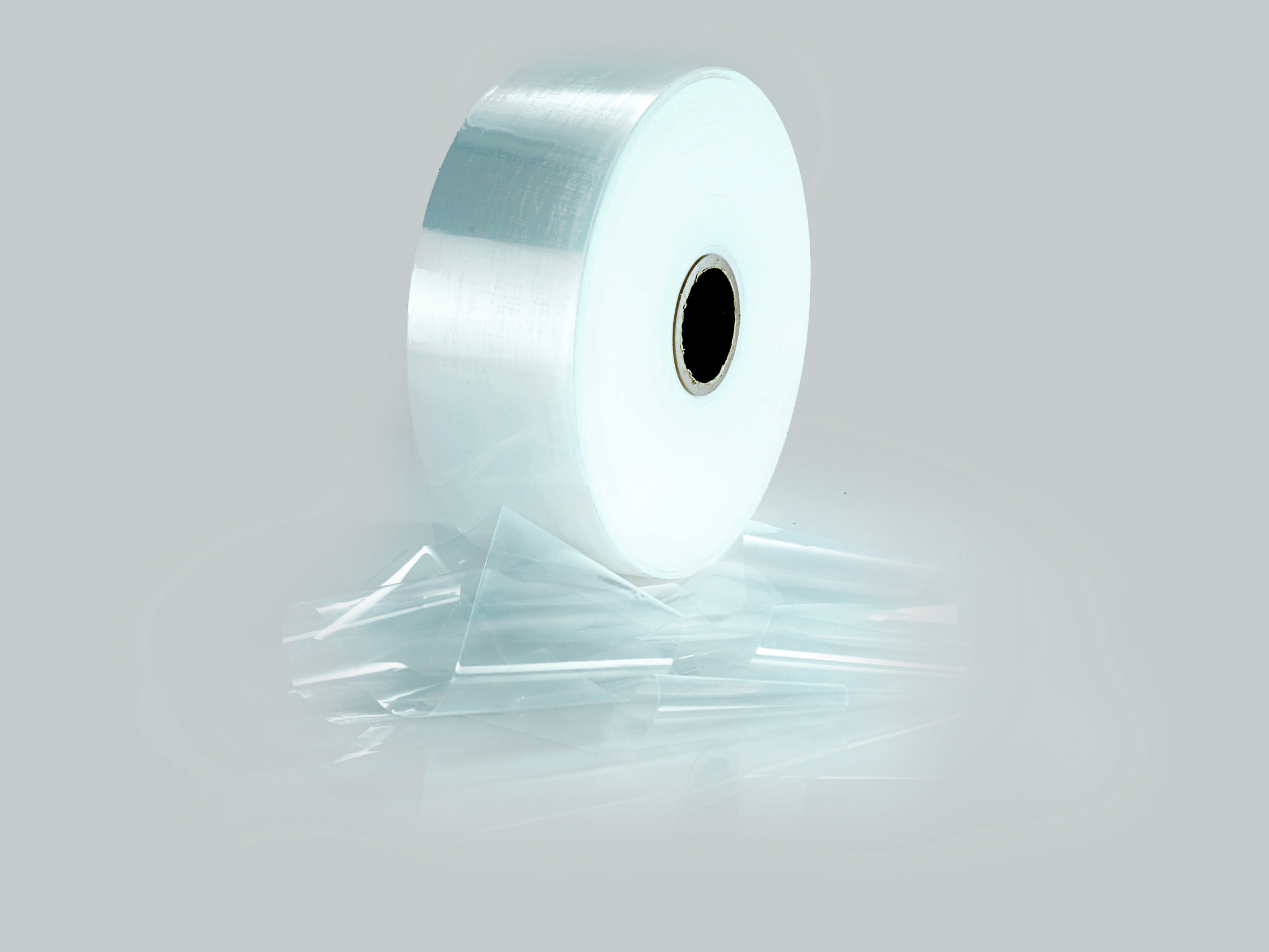
REELS
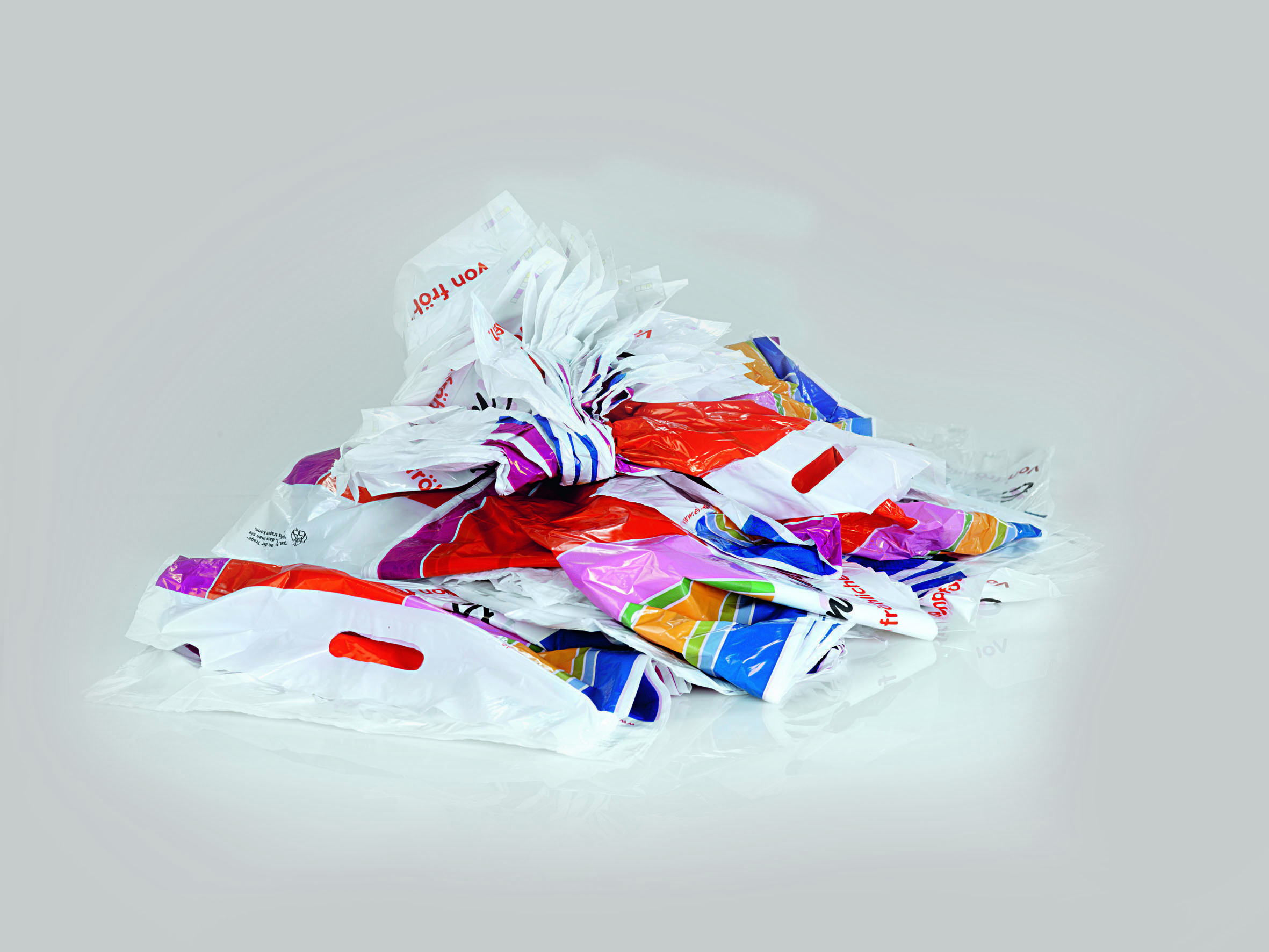
PRINTED
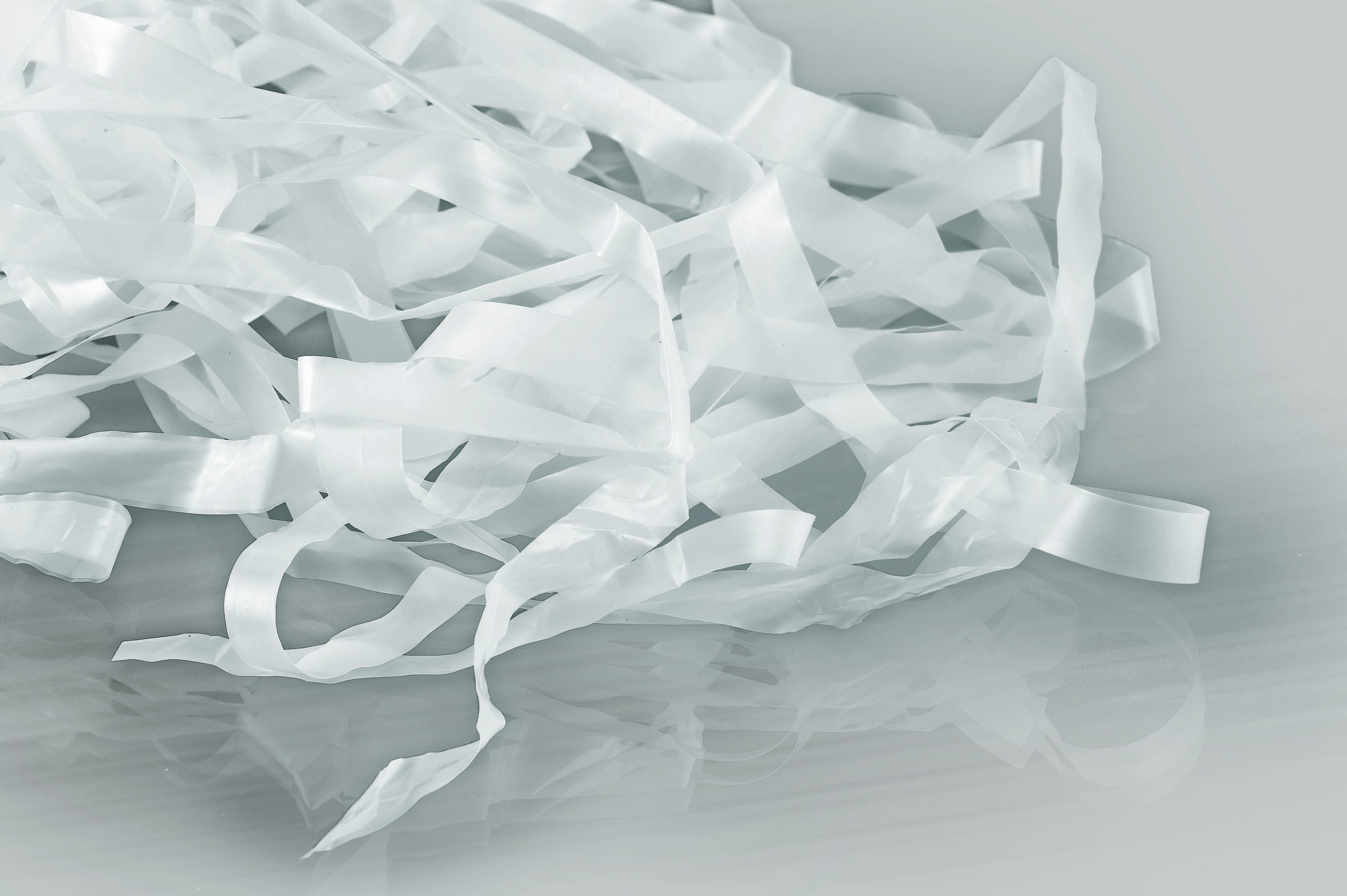
TRIMS
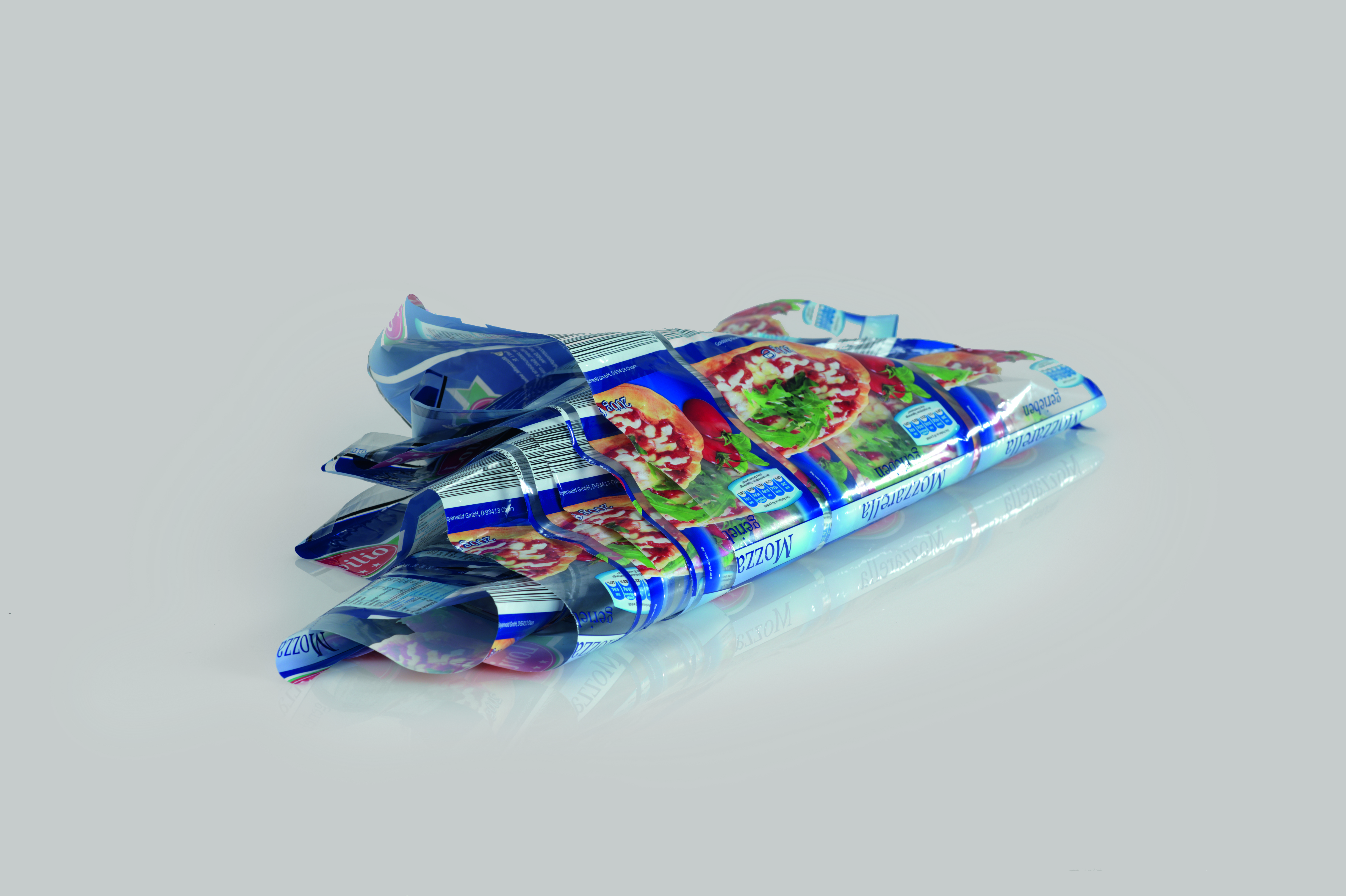
MULTI-LAYER
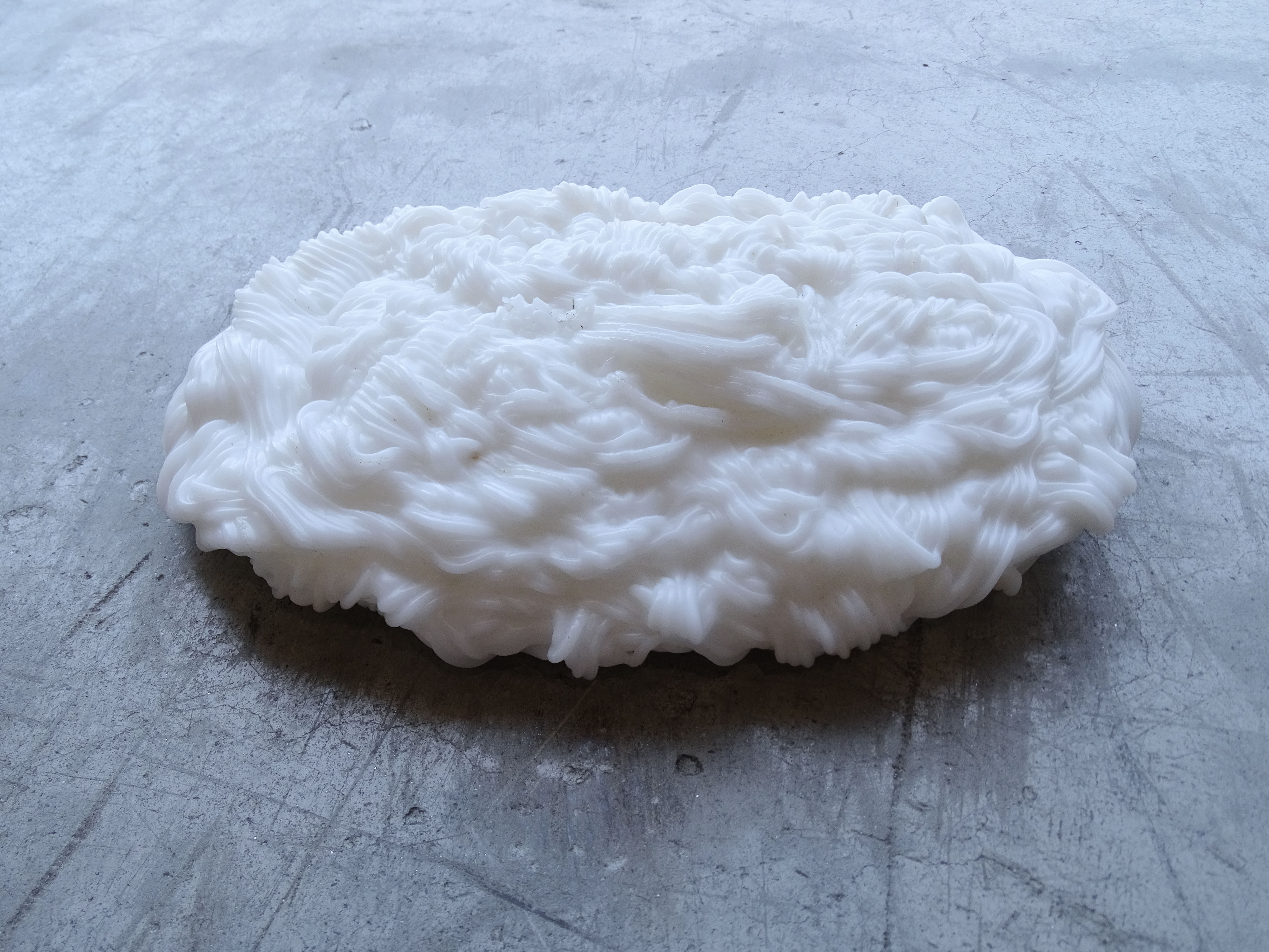
LUMPS
Upload Image...